Origins
Innovation has been a constant part of our business here at Mini Sport. Since our incorporation, (when our founder, Brian Harper, created an improved throttle linkage for the original models), our Mini specialists have regularly pushed the boundaries of automotive design. Each change we’ve made in the machinery, techniques or materials we use has solely been to improve the effectiveness and durability of the parts we manufacture.
One of the major changes we’ve experienced over the years has been the introduction of CNC (Computer-Numerical Control) equipment, leading to us to establish an additional, specialised service – M.A.D (Motor Sport Advanced Development). Proving popular with rallying enthusiasts and restorers alike, M.A.D are able to create replica, improved or even customised parts to optimise the driving experience of the classic Mini.
In 2003, we established M.A.D to work alongside Mini Sport Ltd to supply CNC-produced precision-engineered components for the Mini. Working closely with our in-house technicians and customers, M.A.D has come to understand the engineering requirements of each of our clients, even helping to shape their ideas to create their ideal Mini parts.
3-D Scanning
Often working in conjunction with 3-D printers, the main role of a 3-D scanner is to examine a physical object and send the data to the computer terminal for analysis. This is a particularly useful method to replicate or reimagine old Mini parts – seeing where they’re going wrong or where they can be improved.
Once the data has been received and scrutinised, a Mini specialist can then choose to edit the dimensions on the terminal before starting the 3-D printing process.
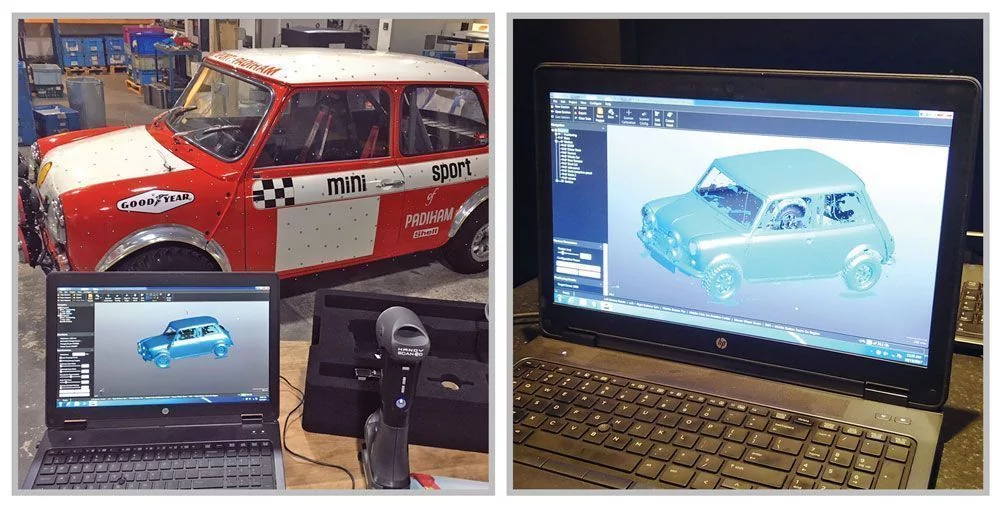
3-D Printing
3-D printers can create pretty much anything you can think of. No matter the shape, size, material or intention of the object you want to make, using the latest software and 3-D printing machinery can make anything from ceramic cups to plastic toys, stoneware vases to fancy chocolate cakes – it’s also becoming possible to create functioning human body parts with 3-D printing!
But we aren’t here to discuss human body parts (a sentence we’d never thought we’ll write!), metal machine parts is what we do – and we make use of a 3-D printer to create them. Replacing the traditional factory production lines, a 3-D printer can create a mechanical part on just a single machine – just like how home inkjet printers replaced ink wells, a printing press, hot metal types and a drying rack.
The process starts by designing a 3-D image on a PC – operators are given instructions by Mini specialist mechanics to understand the dimensions they will need to plot. The object will then be drawn on the computer’s software and the information sent to the 3-D printer for it to be created.
The process is a little like watching a loaf being sliced – but in reverse. Imagine all the slices of a loaf being stacked against each other and combined to create a single object – that’s basically what 3-D printing is. The information given to the printer is of one whole object made from thousands of tiny pieces; the printer recreates this in physical form and builds up the layers, slice by slice. This allows for more precision to be applied – hence why it’s perfect to create moving parts like hinges and wheels.
A particular part that the Mini specialists here at Mini Sport used 3-D printing to create was a Rigid 1 piece alloy calliper; providing the brakes with an enhanced ability to slow the wheels down.
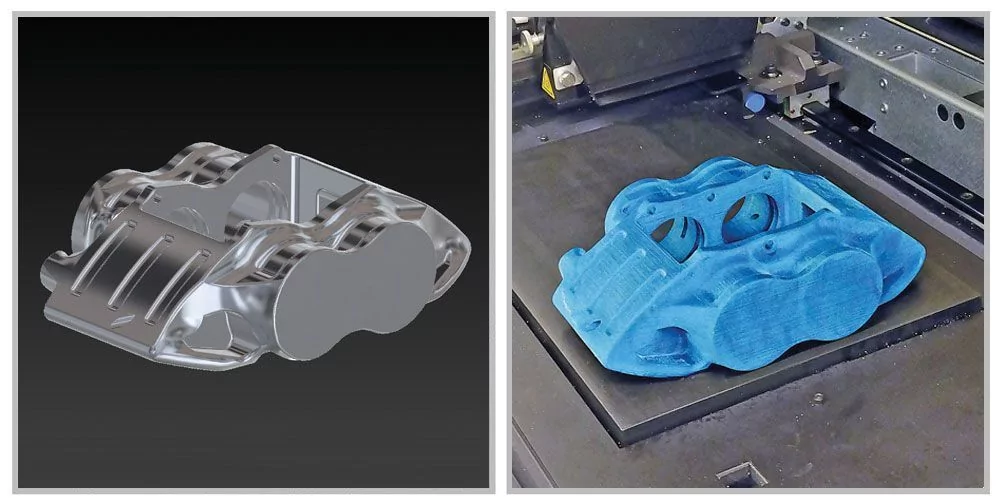
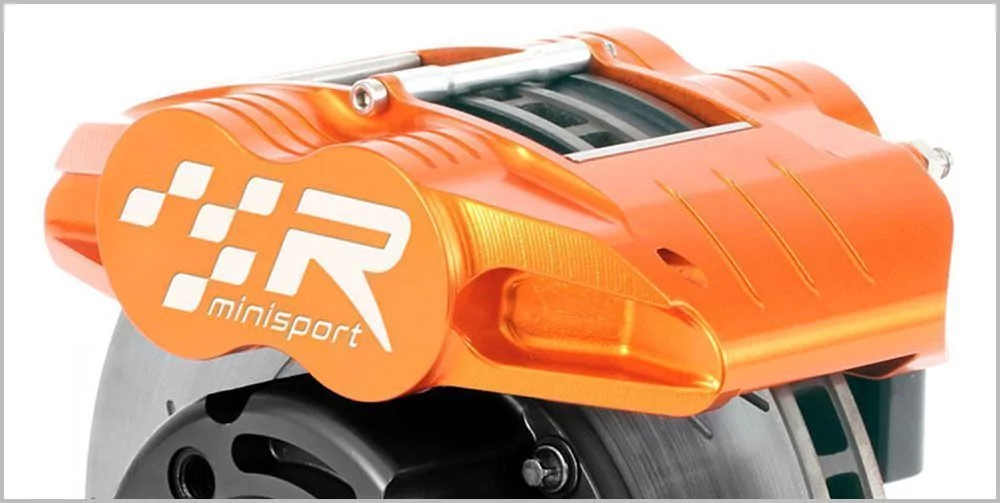